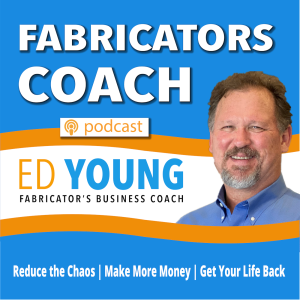
The fewer jobs in your shop (work in process – WIP), the shorter your lead time. Having a lot of jobs in your shop means your lead times may be longer than you like. Lean is a popular process improvement tool and it pushes for the lowest inventory to generate the shortest lead times possible – and, therefore, great competitive advantage. So, if we want short lead times, then this must be the best business solution, right?
WRONG! The lower your WIP levels, the more you are impacted by variation in process performance. Variation comes from:
- Inconsistent machine performance due to wear and tear
- Different process times due to different materials
- Tool wear
- Inconsistent human performance
- Absenteeism
All production operations have inherent variation and, while it can be managed to some degree, this variation cannot be eliminated. Worse still, that variation accumulates through the steps of your fabrication process rather than averaging out. The result is a whip effect that makes it difficult to predict customer install dates. Since this variation can’t be eliminated, lowering WIP too much can hurt your ability to hit your promised install dates and hurt your ability to delight your customer!
Since we can’t completely stop the variation, how do we keep output of the plant consistent so we can meet our promised install dates and still make a profit – all while having short lead times?
Listen to this podcast to hear a discussion of how to get predictability and control of your countertop shop, and additionally, how to increase capacity utilization by 30 percent or more AND shorten your lead time.
The article that is the basis of this recording can be found at: https://www.slipperyrockgazette.net/index.cfm/pageId/4081/Increase%20Inventory%20to%20Increase%20Profit/
No comments yet. Be the first to say something!